अर्धचालक उत्पादन प्रक्रियामा एक महत्वपूर्ण चरणको रूपमा वेफर डाइसिङ प्रविधि, चिप प्रदर्शन, उपज र उत्पादन लागतसँग प्रत्यक्ष रूपमा जोडिएको छ।
#०१ वेफर डाइसिङको पृष्ठभूमि र महत्व
१.१ वेफर डाइसिङको परिभाषा
वेफर डाइसिङ (जसलाई स्क्राइबिङ पनि भनिन्छ) अर्धचालक निर्माणमा एक आवश्यक चरण हो, जसको उद्देश्य प्रशोधित वेफरहरूलाई धेरै व्यक्तिगत डाइसहरूमा विभाजन गर्नु हो। यी डाइसिङहरूमा सामान्यतया पूर्ण सर्किट कार्यक्षमता हुन्छ र अन्ततः इलेक्ट्रोनिक उपकरणहरूको उत्पादनमा प्रयोग हुने मुख्य घटकहरू हुन्। चिप डिजाइनहरू अझ जटिल हुँदै जाँदा र आयामहरू घट्दै जाँदा, वेफर डाइसिङ प्रविधिको लागि परिशुद्धता र दक्षता आवश्यकताहरू बढ्दो रूपमा कडा हुँदै गइरहेका छन्।
व्यावहारिक सञ्चालनहरूमा, वेफर डाइसिङले सामान्यतया उच्च-परिशुद्धता उपकरणहरू जस्तै हीरा ब्लेडहरू प्रयोग गर्दछ जसले प्रत्येक डाई अक्षुण्ण र पूर्ण रूपमा कार्यात्मक रहन्छ भनेर सुनिश्चित गर्दछ। प्रमुख चरणहरूमा काट्नु अघि तयारी, काट्ने प्रक्रियाको क्रममा सटीक नियन्त्रण, र काटिएपछि गुणस्तर निरीक्षण समावेश छ।
काट्नु अघि, वेफरलाई सही काट्ने बाटो सुनिश्चित गर्न चिन्ह लगाइएको र राखिएको हुनुपर्छ। काट्ने क्रममा, वेफरलाई क्षति हुनबाट रोक्नको लागि उपकरणको दबाब र गति जस्ता प्यारामिटरहरूलाई कडाइका साथ नियन्त्रण गर्नुपर्छ। काटिसकेपछि, प्रत्येक चिपले कार्यसम्पादन मापदण्डहरू पूरा गर्छ भनी सुनिश्चित गर्न व्यापक गुणस्तर निरीक्षण गरिन्छ।
वेफर डाइसिङ टेक्नोलोजीका आधारभूत सिद्धान्तहरूले काट्ने उपकरणहरूको छनोट र प्रक्रिया प्यारामिटरहरूको सेटिङ मात्र नभई काट्ने गुणस्तरमा सामग्रीहरूको मेकानिकल गुणहरू र विशेषताहरूको प्रभावलाई पनि समेट्छन्। उदाहरणका लागि, कम-के डाइइलेक्ट्रिक सिलिकन वेफरहरू, तिनीहरूको निम्न मेकानिकल गुणहरूको कारणले, काट्ने क्रममा तनाव एकाग्रताको लागि अत्यधिक संवेदनशील हुन्छन्, जसले गर्दा चिपिङ र क्र्याकिंग जस्ता विफलताहरू निम्त्याउँछन्। कम-के सामग्रीहरूको कम कठोरता र भंगुरताले तिनीहरूलाई मेकानिकल बल वा थर्मल तनाव अन्तर्गत संरचनात्मक क्षतिको लागि बढी प्रवण बनाउँछ, विशेष गरी काट्ने क्रममा। उपकरण र वेफर सतह बीचको सम्पर्क, उच्च तापक्रमसँग मिलेर, तनाव एकाग्रतालाई अझ बढाउन सक्छ।
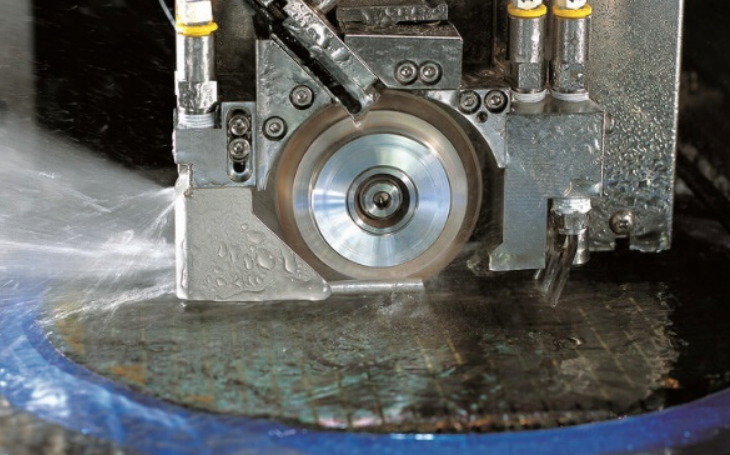
भौतिक विज्ञानमा भएको प्रगतिसँगै, वेफर डाइसिङ प्रविधिले परम्परागत सिलिकन-आधारित अर्धचालकहरूभन्दा बाहिर गएर ग्यालियम नाइट्राइड (GaN) जस्ता नयाँ सामग्रीहरू समावेश गरेको छ। यी नयाँ सामग्रीहरू, तिनीहरूको कठोरता र संरचनात्मक गुणहरूको कारणले गर्दा, डाइसिङ प्रक्रियाहरूको लागि नयाँ चुनौतीहरू खडा गर्छन्, जसलाई काट्ने उपकरणहरू र प्रविधिहरूमा थप सुधारहरू आवश्यक पर्दछ।
अर्धचालक उद्योगमा एक महत्वपूर्ण प्रक्रियाको रूपमा, विकसित मागहरू र प्राविधिक प्रगतिहरूको प्रतिक्रियामा वेफर डाइसिङलाई अनुकूलित गरिँदै छ, जसले भविष्यको माइक्रोइलेक्ट्रोनिक्स र एकीकृत सर्किट प्रविधिहरूको लागि आधार तयार पार्छ।
वेफर डाइसिङ प्रविधिमा भएका सुधारहरू सहायक सामग्री र उपकरणहरूको विकासभन्दा बाहिर जान्छन्। तिनीहरूले प्रक्रिया अनुकूलन, उपकरण प्रदर्शनमा वृद्धि, र डाइसिङ प्यारामिटरहरूको सटीक नियन्त्रण पनि समावेश गर्दछन्। यी प्रगतिहरूले वेफर डाइसिङ प्रक्रियामा उच्च परिशुद्धता, दक्षता र स्थिरता सुनिश्चित गर्ने लक्ष्य राख्छन्, जसले गर्दा अर्धचालक उद्योगको साना आयामहरू, उच्च एकीकरण र थप जटिल चिप संरचनाहरूको आवश्यकता पूरा हुन्छ।
सुधार क्षेत्र | विशिष्ट उपायहरू | प्रभावहरू |
प्रक्रिया अनुकूलन | - प्रारम्भिक तयारीहरू सुधार गर्नुहोस्, जस्तै थप सटीक वेफर स्थिति र मार्ग योजना। | - काट्ने त्रुटिहरू कम गर्नुहोस् र स्थिरता सुधार गर्नुहोस्। |
- काट्ने त्रुटिहरू कम गर्नुहोस् र स्थिरता बढाउनुहोस्। | - उपकरणको दबाब, गति र तापक्रम समायोजन गर्न वास्तविक-समय अनुगमन र प्रतिक्रिया संयन्त्र अपनाउनुहोस्। | |
- वेफर ब्रेकेज दर कम गर्नुहोस् र चिपको गुणस्तर सुधार गर्नुहोस्। | ||
उपकरण प्रदर्शन वृद्धि | - उच्च-परिशुद्धता मेकानिकल प्रणाली र उन्नत स्वचालन नियन्त्रण प्रविधि प्रयोग गर्नुहोस्। | - काट्ने शुद्धता बढाउनुहोस् र सामग्रीको बर्बादी कम गर्नुहोस्। |
- उच्च-कठोरता सामग्री वेफरहरूको लागि उपयुक्त लेजर काट्ने प्रविधि परिचय गर्नुहोस्। | - उत्पादन दक्षता सुधार गर्नुहोस् र म्यानुअल त्रुटिहरू कम गर्नुहोस्। | |
- स्वचालित अनुगमन र समायोजनको लागि उपकरण स्वचालन बढाउनुहोस्। | ||
सटीक प्यारामिटर नियन्त्रण | - काट्ने गहिराइ, गति, उपकरणको प्रकार, र शीतलन विधिहरू जस्ता प्यारामिटरहरू राम्ररी समायोजन गर्नुहोस्। | - डाइ अखण्डता र विद्युतीय कार्यसम्पादन सुनिश्चित गर्नुहोस्। |
- वेफर सामग्री, मोटाई, र संरचनाको आधारमा प्यारामिटरहरू अनुकूलित गर्नुहोस्। | - उत्पादन दर बढाउने, भौतिक फोहोर घटाउने र उत्पादन लागत कम गर्ने। | |
रणनीतिक महत्व | - बजारको माग पूरा गर्न निरन्तर नयाँ प्राविधिक मार्गहरू अन्वेषण गर्नुहोस्, प्रक्रियाहरूलाई अनुकूलन गर्नुहोस्, र उपकरण क्षमताहरू बढाउनुहोस्। | - नयाँ सामग्री र उन्नत चिप डिजाइनहरूको विकासलाई समर्थन गर्दै, चिप उत्पादन उपज र कार्यसम्पादन सुधार गर्नुहोस्। |
१.२ वेफर डाइसिङको महत्त्व
अर्धचालक निर्माण प्रक्रियामा वेफर डाइसिङले महत्त्वपूर्ण भूमिका खेल्छ, जसले पछिल्ला चरणहरू साथै अन्तिम उत्पादनको गुणस्तर र कार्यसम्पादनमा प्रत्यक्ष प्रभाव पार्छ। यसको महत्त्वलाई निम्नानुसार विस्तृत रूपमा वर्णन गर्न सकिन्छ:
पहिलो, डाइसिङको शुद्धता र स्थिरता चिप उपज र विश्वसनीयता सुनिश्चित गर्नको लागि महत्वपूर्ण छ। निर्माणको क्रममा, वेफरहरूले धेरै जटिल सर्किट संरचनाहरू बनाउन धेरै प्रशोधन चरणहरू पार गर्छन्, जुन व्यक्तिगत चिप्स (डाइज) मा ठ्याक्कै विभाजित हुनुपर्छ। यदि डाइसिङ प्रक्रियाको क्रममा पङ्क्तिबद्धता वा काट्ने क्रममा महत्त्वपूर्ण त्रुटिहरू छन् भने, सर्किटहरू क्षतिग्रस्त हुन सक्छन्, जसले चिपको कार्यक्षमता र विश्वसनीयतालाई असर गर्छ। त्यसकारण, उच्च-परिशुद्धता डाइसिङ प्रविधिले प्रत्येक चिपको अखण्डता सुनिश्चित मात्र गर्दैन तर समग्र उपज दरमा सुधार गर्दै आन्तरिक सर्किटहरूमा हुने क्षतिलाई पनि रोक्छ।
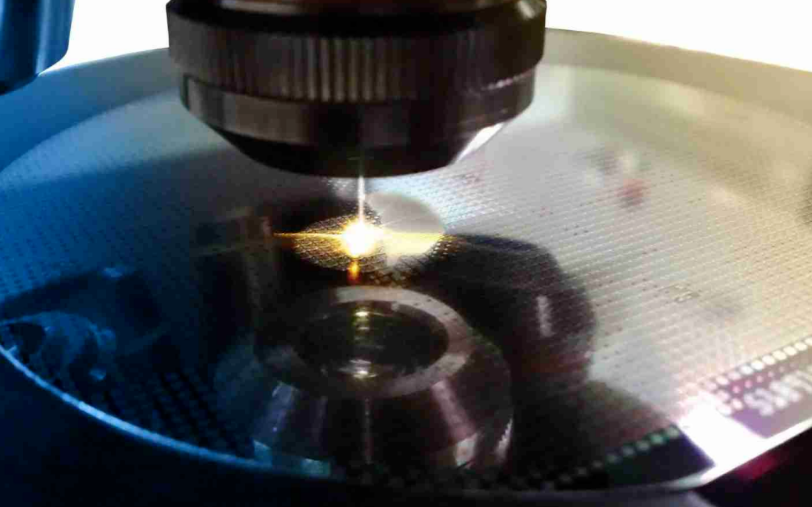
दोस्रो, वेफर डाइसिङले उत्पादन दक्षता र लागत नियन्त्रणमा महत्त्वपूर्ण प्रभाव पार्छ। उत्पादन प्रक्रियामा एक महत्त्वपूर्ण चरणको रूपमा, यसको दक्षताले त्यसपछिका चरणहरूको प्रगतिलाई प्रत्यक्ष रूपमा असर गर्छ। डाइसिङ प्रक्रियालाई अनुकूलन गरेर, स्वचालन स्तर बढाएर, र काट्ने गति सुधार गरेर, समग्र उत्पादन दक्षतालाई धेरै बढाउन सकिन्छ।
अर्कोतर्फ, डाइसिङको समयमा हुने सामग्रीको बर्बादी लागत व्यवस्थापनको लागि एक महत्वपूर्ण कारक हो। उन्नत डाइसिङ प्रविधिहरूको प्रयोगले काट्ने प्रक्रियाको क्रममा अनावश्यक सामग्रीको क्षति मात्र कम गर्दैन तर वेफरको उपयोग पनि बढाउँछ, जसले गर्दा उत्पादन लागत घट्छ।
अर्धचालक प्रविधिमा भएको प्रगतिसँगै, वेफरको व्यास बढ्दै जान्छ, र सर्किट घनत्व तदनुसार बढ्दै जान्छ, जसले गर्दा डाइसिङ प्रविधिमा उच्च माग हुन्छ। ठूला वेफरहरूलाई काट्ने मार्गहरूको थप सटीक नियन्त्रण चाहिन्छ, विशेष गरी उच्च-घनत्व सर्किट क्षेत्रहरूमा, जहाँ सानो विचलनले पनि धेरै चिपहरूलाई दोषपूर्ण बनाउन सक्छ। थप रूपमा, ठूला वेफरहरूमा थप काट्ने लाइनहरू र थप जटिल प्रक्रिया चरणहरू समावेश हुन्छन्, जसले गर्दा यी चुनौतीहरू पूरा गर्न डाइसिङ प्रविधिहरूको परिशुद्धता, स्थिरता र दक्षतामा थप सुधारहरू आवश्यक पर्दछ।
१.३ वेफर डाइसिङ प्रक्रिया
वेफर डाइसिङ प्रक्रियाले तयारी चरणदेखि अन्तिम गुणस्तर निरीक्षणसम्मका सबै चरणहरू समेट्छ, प्रत्येक चरण डाइस गरिएका चिप्सको गुणस्तर र कार्यसम्पादन सुनिश्चित गर्न महत्त्वपूर्ण हुन्छ। तल प्रत्येक चरणको विस्तृत व्याख्या दिइएको छ।
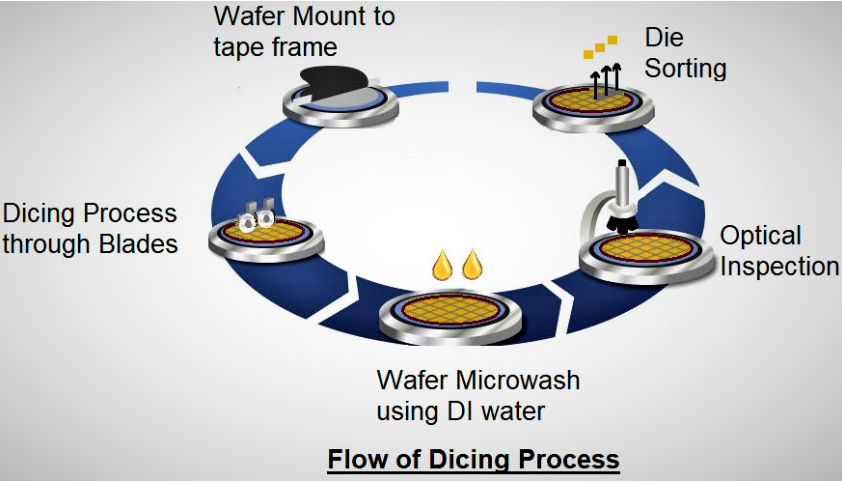
चरण | विस्तृत विवरण |
तयारी चरण | -वेफर सफाई: सफा सतह सुनिश्चित गर्दै अशुद्धता, कण र प्रदूषकहरू हटाउन उच्च शुद्धता भएको पानी र विशेष सफाई एजेन्टहरू, अल्ट्रासोनिक वा मेकानिकल स्क्रबिङसँग मिलाएर प्रयोग गर्नुहोस्। -सटीक स्थिति निर्धारण: डिजाइन गरिएको काट्ने बाटोहरूमा वेफरलाई सही रूपमा विभाजित गरिएको छ भनी सुनिश्चित गर्न उच्च-परिशुद्धता उपकरणहरू प्रयोग गर्नुहोस्। -वेफर फिक्सेसन: काट्ने क्रममा स्थिरता कायम राख्न, कम्पन वा चालबाट हुने क्षतिलाई रोक्न वेफरलाई टेप फ्रेममा सुरक्षित गर्नुहोस्। |
काट्ने चरण | -ब्लेड डाइसिङ: भौतिक काटनको लागि उच्च-गतिको घुम्ने हीरा-लेपित ब्लेडहरू प्रयोग गर्नुहोस्, सिलिकन-आधारित सामग्रीहरूको लागि उपयुक्त र लागत-प्रभावी। -लेजर डाइसिङ: गैर-सम्पर्क काटनको लागि उच्च-ऊर्जा लेजर बीमहरू प्रयोग गर्नुहोस्, ग्यालियम नाइट्राइड जस्ता भंगुर वा उच्च-कठोरता सामग्रीहरूको लागि आदर्श, उच्च परिशुद्धता र कम सामग्री क्षति प्रदान गर्दछ। -नयाँ प्रविधिहरू: गर्मीबाट प्रभावित क्षेत्रहरूलाई न्यूनीकरण गर्दै दक्षता र शुद्धतामा थप सुधार गर्न लेजर र प्लाज्मा काट्ने प्रविधिहरू परिचय गराउनुहोस्। |
सफाई चरण | - काट्ने क्रममा उत्पन्न हुने फोहोर र धुलो हटाउन, पछिल्ला प्रक्रियाहरू वा चिप विद्युतीय कार्यसम्पादनलाई असर गर्नबाट अवशेषहरूलाई रोक्न, अल्ट्रासोनिक वा स्प्रे क्लिनिङसँग मिलाएर डिआयोनाइज्ड पानी (DI पानी) र विशेष सफाई एजेन्टहरू प्रयोग गर्नुहोस्। - उच्च शुद्धता भएको DI पानीले नयाँ दूषित पदार्थहरू भित्रिनबाट जोगाउँछ, सफा वेफर वातावरण सुनिश्चित गर्दछ। |
निरीक्षण चरण | -अप्टिकल निरीक्षण: AI एल्गोरिदमसँग मिलेर अप्टिकल पत्ता लगाउने प्रणालीहरू प्रयोग गर्नुहोस् जसले गर्दा दोषहरू छिटो पहिचान गर्न सकिन्छ, काटिएका चिप्समा कुनै दरार वा चिपिङ नहोस् भन्ने कुरा सुनिश्चित हुन्छ, निरीक्षण दक्षतामा सुधार हुन्छ, र मानवीय त्रुटि कम हुन्छ। -आयाम मापन: चिप आयामहरूले डिजाइन विशिष्टताहरू पूरा गर्छन् भनी प्रमाणित गर्नुहोस्। -विद्युतीय प्रदर्शन परीक्षण: महत्वपूर्ण चिप्सको विद्युतीय कार्यसम्पादनले मापदण्डहरू पूरा गर्छ भनी सुनिश्चित गर्नुहोस्, जसले गर्दा पछिल्ला अनुप्रयोगहरूमा विश्वसनीयताको ग्यारेन्टी हुन्छ। |
क्रमबद्ध चरण | - टेप फ्रेमबाट योग्य चिप्स अलग गर्न रोबोटिक आर्म्स वा भ्याकुम सक्सन कप प्रयोग गर्नुहोस् र कार्यसम्पादनको आधारमा स्वचालित रूपमा क्रमबद्ध गर्नुहोस्, उत्पादन दक्षता र लचिलोपन सुनिश्चित गर्दै परिशुद्धता सुधार गर्नुहोस्। |
वेफर काट्ने प्रक्रियामा वेफर सफा गर्ने, स्थिति निर्धारण गर्ने, काट्ने, सफा गर्ने, निरीक्षण गर्ने र क्रमबद्ध गर्ने काम समावेश हुन्छ, जसमा प्रत्येक चरण महत्वपूर्ण हुन्छ। स्वचालन, लेजर काट्ने, र एआई निरीक्षण प्रविधिहरूमा भएको प्रगतिसँगै, आधुनिक वेफर काट्ने प्रणालीहरूले उच्च परिशुद्धता, गति र कम सामग्री हानि हासिल गर्न सक्छन्। भविष्यमा, लेजर र प्लाज्मा जस्ता नयाँ काट्ने प्रविधिहरूले बढ्दो जटिल चिप डिजाइनहरूको आवश्यकताहरू पूरा गर्न परम्परागत ब्लेड काट्नेलाई बिस्तारै प्रतिस्थापन गर्नेछन्, जसले अर्धचालक उत्पादन प्रक्रियाहरूको विकासलाई अगाडि बढाउनेछ।
वेफर काट्ने प्रविधि र यसका सिद्धान्तहरू
यो तस्बिरले तीन सामान्य वेफर काट्ने प्रविधिहरू चित्रण गर्दछ:ब्लेड डाइसिङ,लेजर डाइसिङ, रप्लाज्मा डाइसिङतल यी तीन प्रविधिहरूको विस्तृत विश्लेषण र पूरक व्याख्या दिइएको छ:
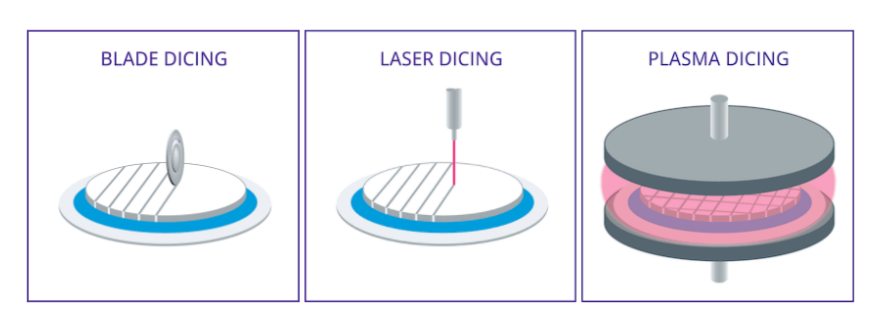
अर्धचालक निर्माणमा, वेफर काट्ने काम एउटा महत्त्वपूर्ण चरण हो जसमा वेफरको मोटाईको आधारमा उपयुक्त काट्ने विधि चयन गर्न आवश्यक पर्दछ। पहिलो चरण भनेको वेफरको मोटाई निर्धारण गर्नु हो। यदि वेफरको मोटाई १०० माइक्रोन भन्दा बढी छ भने, ब्लेड डाइसिङलाई काट्ने विधिको रूपमा छनौट गर्न सकिन्छ। यदि ब्लेड डाइसिङ उपयुक्त छैन भने, फ्र्याक्चर डाइसिङ विधि प्रयोग गर्न सकिन्छ, जसमा स्क्राइब काट्ने र ब्लेड डाइसिङ प्रविधि दुवै समावेश छन्।
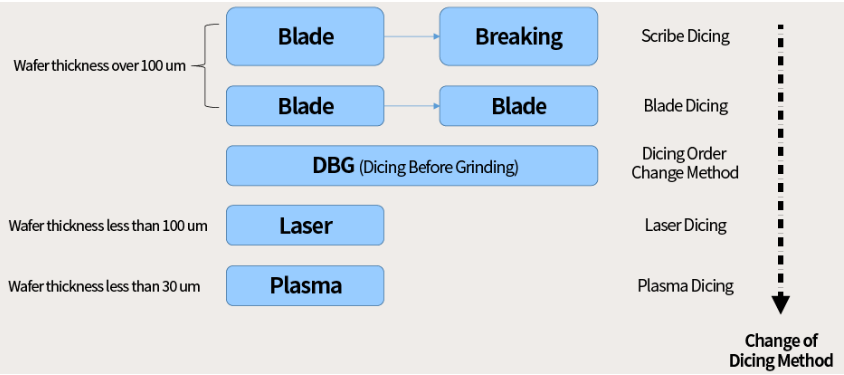
जब वेफरको मोटाई ३० र १०० माइक्रोन बीच हुन्छ, DBG (ग्राइन्डिङ अघि पासा) विधि सिफारिस गरिन्छ। यस अवस्थामा, उत्तम परिणामहरू प्राप्त गर्न स्क्राइब काट्ने, ब्लेड डाइसिङ गर्ने, वा आवश्यकता अनुसार काट्ने अनुक्रम समायोजन गर्ने छनौट गर्न सकिन्छ।
३० माइक्रोन भन्दा कम मोटाई भएका अल्ट्रा-थिन वेफरहरूको लागि, अत्यधिक क्षति नगरी पातलो वेफरहरूलाई सटीक रूपमा काट्ने क्षमताको कारणले लेजर काट्ने रुचाइएको विधि बन्छ। यदि लेजर काट्नेले विशिष्ट आवश्यकताहरू पूरा गर्न सक्दैन भने, प्लाज्मा काट्ने विकल्पको रूपमा प्रयोग गर्न सकिन्छ। यो फ्लोचार्टले विभिन्न मोटाई अवस्थाहरूमा सबैभन्दा उपयुक्त वेफर काट्ने प्रविधि छनौट गरिएको सुनिश्चित गर्न स्पष्ट निर्णय लिने मार्ग प्रदान गर्दछ।
२.१ मेकानिकल काट्ने प्रविधि
वेफर डाइसिङमा मेकानिकल काट्ने प्रविधि परम्परागत विधि हो। मुख्य सिद्धान्त भनेको वेफरलाई काट्नको लागि काट्ने उपकरणको रूपमा उच्च-गतिको घुम्ने हीरा ग्राइन्डिङ ह्वील प्रयोग गर्नु हो। मुख्य उपकरणहरूमा हावा-बेयरिङ स्पिन्डल समावेश छ, जसले पूर्वनिर्धारित काट्ने मार्गमा सटीक काट्ने वा ग्रुभिङ गर्न उच्च गतिमा हीरा ग्राइन्डिङ ह्वील उपकरण चलाउँछ। यो प्रविधि यसको कम लागत, उच्च दक्षता, र व्यापक प्रयोज्यताको कारण उद्योगमा व्यापक रूपमा प्रयोग गरिन्छ।
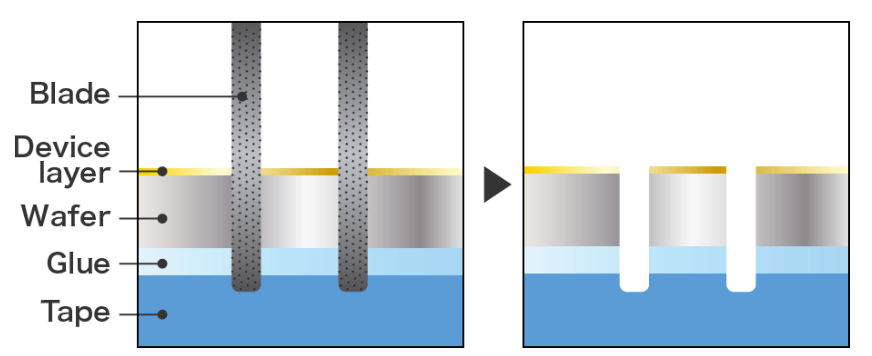
फाइदाहरू
हीरा पिस्ने पाङ्ग्रा उपकरणहरूको उच्च कठोरता र पहिरन प्रतिरोधले मेकानिकल काट्ने प्रविधिलाई विभिन्न वेफर सामग्रीहरूको काट्ने आवश्यकताहरू अनुकूलन गर्न सक्षम बनाउँछ, चाहे परम्परागत सिलिकन-आधारित सामग्रीहरू होस् वा नयाँ कम्पाउन्ड अर्धचालकहरू। यसको सञ्चालन सरल छ, अपेक्षाकृत कम प्राविधिक आवश्यकताहरू सहित, यसले ठूलो उत्पादनमा यसको लोकप्रियतालाई अझ बढावा दिन्छ। थप रूपमा, लेजर काट्ने जस्ता अन्य काट्ने विधिहरूको तुलनामा, मेकानिकल काट्ने लागतहरू बढी नियन्त्रणयोग्य हुन्छन्, जसले यसलाई उच्च-मात्रा उत्पादन आवश्यकताहरूको लागि उपयुक्त बनाउँछ।
सीमाहरू
यसका धेरै फाइदाहरूको बावजुद, मेकानिकल काट्ने प्रविधिका पनि सीमितताहरू छन्। पहिलो, उपकरण र वेफर बीचको भौतिक सम्पर्कको कारण, काट्ने शुद्धता अपेक्षाकृत सीमित छ, जसले गर्दा प्रायः आयामी विचलनहरू हुन्छन् जसले पछिल्ला चिप प्याकेजिङ र परीक्षणको शुद्धतालाई असर गर्न सक्छ। दोस्रो, मेकानिकल काट्ने प्रक्रियाको क्रममा चिपिङ र क्र्याक जस्ता दोषहरू सजिलै हुन सक्छन्, जसले उत्पादन दरलाई मात्र असर गर्दैन तर चिप्सको विश्वसनीयता र आयुमा पनि नकारात्मक असर पार्न सक्छ। मेकानिकल तनाव-प्रेरित क्षति उच्च-घनत्व चिप निर्माणको लागि विशेष गरी हानिकारक छ, विशेष गरी भंगुर सामग्रीहरू काट्दा, जहाँ यी समस्याहरू बढी प्रमुख हुन्छन्।
प्राविधिक सुधारहरू
यी सीमितताहरू पार गर्न, अनुसन्धानकर्ताहरूले मेकानिकल काट्ने प्रक्रियालाई निरन्तर अनुकूलन गरिरहेका छन्। प्रमुख सुधारहरूमा काट्ने परिशुद्धता र टिकाउपन सुधार गर्न ग्राइन्डिङ ह्वीलहरूको डिजाइन र सामग्री चयन बढाउनु समावेश छ। थप रूपमा, काट्ने उपकरणहरूको संरचनात्मक डिजाइन र नियन्त्रण प्रणालीहरूलाई अनुकूलन गर्नाले काट्ने प्रक्रियाको स्थिरता र स्वचालनमा अझ सुधार आएको छ। यी प्रगतिहरूले मानव सञ्चालनबाट हुने त्रुटिहरूलाई कम गर्छ र काट्नेहरूको स्थिरतामा सुधार गर्छ। काट्ने प्रक्रियाको क्रममा विसंगतिहरूको वास्तविक-समय निगरानीको लागि उन्नत निरीक्षण र गुणस्तर नियन्त्रण प्रविधिहरूको परिचयले काट्ने विश्वसनीयता र उपजमा पनि उल्लेखनीय सुधार गरेको छ।
भविष्यको विकास र नयाँ प्रविधिहरू
यद्यपि मेकानिकल काट्ने प्रविधिले अझै पनि वेफर काट्ने काममा महत्त्वपूर्ण स्थान राख्छ, अर्धचालक प्रक्रियाहरू विकसित हुँदै जाँदा नयाँ काट्ने प्रविधिहरू द्रुत गतिमा अगाडि बढिरहेका छन्। उदाहरणका लागि, थर्मल लेजर काट्ने प्रविधिको प्रयोगले मेकानिकल काट्ने काममा परिशुद्धता र दोष समस्याहरूको लागि नयाँ समाधान प्रदान गर्दछ। यो गैर-सम्पर्क काट्ने विधिले वेफरमा भौतिक तनाव कम गर्छ, चिपिङ र क्र्याकिंगको घटनालाई उल्लेखनीय रूपमा कम गर्छ, विशेष गरी जब बढी भंगुर सामग्रीहरू काटिन्छ। भविष्यमा, उदीयमान काट्ने प्रविधिहरूसँग मेकानिकल काट्ने प्रविधिको एकीकरणले अर्धचालक उत्पादनलाई थप विकल्पहरू र लचिलोपन प्रदान गर्नेछ, जसले गर्दा उत्पादन दक्षता र चिप गुणस्तर अझ बढ्नेछ।
निष्कर्षमा, मेकानिकल काट्ने प्रविधिमा केही कमजोरीहरू भए तापनि, निरन्तर प्राविधिक सुधारहरू र नयाँ काट्ने प्रविधिहरूसँग यसको एकीकरणले यसलाई अझै पनि अर्धचालक निर्माणमा महत्त्वपूर्ण भूमिका खेल्न र भविष्यका प्रक्रियाहरूमा यसको प्रतिस्पर्धात्मकता कायम राख्न अनुमति दिन्छ।
२.२ लेजर काट्ने प्रविधि
वेफर काट्ने नयाँ विधिको रूपमा लेजर काट्ने प्रविधिले यसको उच्च परिशुद्धता, मेकानिकल सम्पर्क क्षतिको अभाव र द्रुत काट्ने क्षमताहरूको कारणले अर्धचालक उद्योगमा बिस्तारै व्यापक ध्यान आकर्षित गरेको छ। यो प्रविधिले वेफर सामग्रीको सतहमा सानो ताप-प्रभावित क्षेत्र सिर्जना गर्न लेजर बीमको उच्च ऊर्जा घनत्व र फोकस गर्ने क्षमता प्रयोग गर्दछ। जब लेजर बीम वेफरमा लागू गरिन्छ, उत्पन्न हुने थर्मल तनावले तोकिएको स्थानमा सामग्रीलाई फ्र्याक्चर गर्दछ, सटीक काट्ने प्राप्त गर्दछ।
लेजर काट्ने प्रविधिका फाइदाहरू
• उच्च परिशुद्धता: लेजर बीमको सटीक स्थिति क्षमताले आधुनिक उच्च-परिशुद्धता, उच्च-घनत्व एकीकृत सर्किट निर्माणको आवश्यकताहरू पूरा गर्दै माइक्रोन वा न्यानोमिटर-स्तरको काट्ने परिशुद्धताको लागि अनुमति दिन्छ।
• कुनै यान्त्रिक सम्पर्क छैन: लेजर काट्नेले वेफरसँग भौतिक सम्पर्कबाट बचाउँछ, चिपिङ र क्र्याकिङ जस्ता मेकानिकल काट्ने सामान्य समस्याहरूलाई रोक्छ, जसले गर्दा चिप्सको उत्पादन दर र विश्वसनीयतामा उल्लेखनीय सुधार हुन्छ।
• छिटो काट्ने गति: लेजर काट्ने उच्च गतिले उत्पादन दक्षता बढाउन योगदान पुर्याउँछ, जसले गर्दा यसलाई विशेष गरी ठूला-स्तरीय, उच्च-गति उत्पादन परिदृश्यहरूको लागि उपयुक्त बनाउँछ।
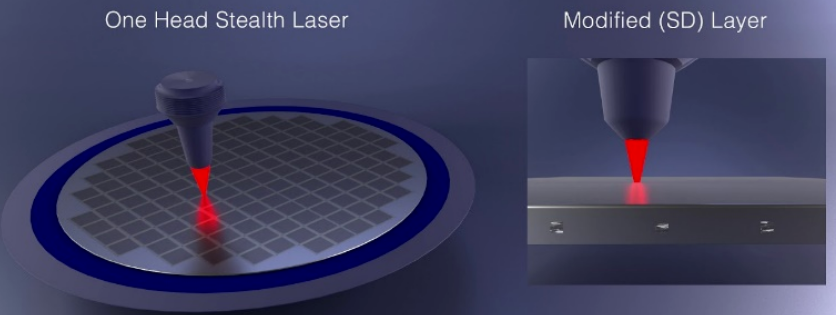
सामना गरिएका चुनौतीहरू
• उच्च उपकरण लागत: लेजर काट्ने उपकरणको लागि प्रारम्भिक लगानी उच्च छ, जसले आर्थिक दबाब प्रस्तुत गर्दछ, विशेष गरी साना देखि मध्यम आकारका उत्पादन उद्यमहरूको लागि।
• जटिल प्रक्रिया नियन्त्रण: लेजर काट्ने कामलाई ऊर्जा घनत्व, फोकस स्थिति, र काट्ने गति सहित धेरै प्यारामिटरहरूको सटीक नियन्त्रण आवश्यक पर्दछ, जसले प्रक्रियालाई जटिल बनाउँछ।
• गर्मी प्रभावित क्षेत्रका समस्याहरू: लेजर काट्नेको सम्पर्करहित प्रकृतिले मेकानिकल क्षति कम गर्छ, ताप-प्रभावित क्षेत्र (HAZ) को कारणले हुने थर्मल तनावले वेफर सामग्रीको गुणहरूलाई नकारात्मक रूपमा असर गर्न सक्छ। यो प्रभावलाई कम गर्न प्रक्रियाको थप अनुकूलन आवश्यक छ।
प्राविधिक सुधार निर्देशनहरू
यी चुनौतीहरूलाई सम्बोधन गर्न, अनुसन्धानकर्ताहरूले उपकरणको लागत घटाउने, कटौती दक्षता सुधार गर्ने र प्रक्रिया प्रवाहलाई अनुकूलन गर्ने कुरामा ध्यान केन्द्रित गरिरहेका छन्।
• कुशल लेजर र अप्टिकल प्रणालीहरू: अझ कुशल लेजरहरू र उन्नत अप्टिकल प्रणालीहरू विकास गरेर, काट्ने परिशुद्धता र गति बढाउँदै उपकरण लागत घटाउन सम्भव छ।
• प्रक्रिया प्यारामिटरहरू अनुकूलन गर्दै: गर्मीबाट प्रभावित क्षेत्रलाई कम गर्ने प्रक्रियाहरूमा सुधार गर्न लेजरहरू र वेफर सामग्रीहरू बीचको अन्तरक्रियामा गहन अनुसन्धान भइरहेको छ, जसले गर्दा काटनको गुणस्तरमा सुधार हुन्छ।
• बुद्धिमान नियन्त्रण प्रणालीहरू: बुद्धिमान नियन्त्रण प्रविधिहरूको विकासले लेजर काट्ने प्रक्रियालाई स्वचालित र अनुकूलन गर्ने, यसको स्थिरता र स्थिरतामा सुधार गर्ने लक्ष्य राख्छ।
लेजर काट्ने प्रविधि अति-पातलो वेफर र उच्च-परिशुद्धता काट्ने परिदृश्यहरूमा विशेष गरी प्रभावकारी छ। वेफरको आकार बढ्दै जाँदा र सर्किट घनत्व बढ्दै जाँदा, परम्परागत मेकानिकल काट्ने विधिहरूले आधुनिक अर्धचालक निर्माणको उच्च-परिशुद्धता र उच्च-दक्षता मागहरू पूरा गर्न संघर्ष गर्छन्। यसको अद्वितीय फाइदाहरूको कारण, लेजर काट्ने यी क्षेत्रहरूमा रुचाइएको समाधान बन्दै गइरहेको छ।
लेजर काट्ने प्रविधिले अझै पनि उच्च उपकरण लागत र प्रक्रिया जटिलता जस्ता चुनौतीहरूको सामना गरिरहेको भए तापनि, उच्च परिशुद्धता र गैर-सम्पर्क क्षतिमा यसको अद्वितीय फाइदाहरूले यसलाई अर्धचालक निर्माणमा विकासको लागि महत्त्वपूर्ण दिशा बनाउँछ। लेजर प्रविधि र बुद्धिमान नियन्त्रण प्रणालीहरू अगाडि बढ्दै जाँदा, लेजर काट्नेले वेफर काट्ने दक्षता र गुणस्तरमा अझ सुधार गर्ने अपेक्षा गरिएको छ, जसले अर्धचालक उद्योगको निरन्तर विकासलाई अगाडि बढाउँछ।
२.३ प्लाज्मा काट्ने प्रविधि
प्लाज्मा काट्ने प्रविधि, एक उदीयमान वेफर डाइसिङ विधिको रूपमा, हालका वर्षहरूमा उल्लेखनीय ध्यान आकर्षित गरेको छ। यो प्रविधिले प्लाज्मा बीमको ऊर्जा, गति र काट्ने मार्गलाई नियन्त्रण गरेर वेफरहरूलाई सटीक रूपमा काट्न उच्च-ऊर्जा प्लाज्मा बीमहरू प्रयोग गर्दछ, इष्टतम काट्ने परिणामहरू प्राप्त गर्दछ।
काम गर्ने सिद्धान्त र फाइदाहरू
प्लाज्मा काट्ने प्रक्रिया उपकरणद्वारा उत्पन्न हुने उच्च-तापमान, उच्च-ऊर्जा प्लाज्मा बीममा निर्भर गर्दछ। यो बीमले धेरै छोटो समयमा वेफर सामग्रीलाई यसको पग्लने वा वाष्पीकरण बिन्दुमा तताउन सक्छ, जसले गर्दा छिटो काट्न सकिन्छ। परम्परागत मेकानिकल वा लेजर काट्नेको तुलनामा, प्लाज्मा काट्ने छिटो हुन्छ र सानो ताप-प्रभावित क्षेत्र उत्पादन गर्दछ, जसले गर्दा काट्ने क्रममा दरार र क्षतिको घटनालाई प्रभावकारी रूपमा कम गर्दछ।
व्यावहारिक अनुप्रयोगहरूमा, प्लाज्मा काट्ने प्रविधि विशेष गरी जटिल आकारका वेफरहरू ह्यान्डल गर्नमा माहिर छ। यसको उच्च-ऊर्जा, समायोज्य प्लाज्मा बीमले उच्च परिशुद्धताका साथ अनियमित आकारका वेफरहरू सजिलै काट्न सक्छ। त्यसकारण, माइक्रोइलेक्ट्रोनिक्स निर्माणमा, विशेष गरी उच्च-अन्त चिपहरूको अनुकूलित र सानो-ब्याच उत्पादनमा, यो प्रविधिले व्यापक प्रयोगको लागि ठूलो आशा देखाउँछ।
चुनौती र सीमितताहरू
प्लाज्मा काट्ने प्रविधिका धेरै फाइदाहरू भए तापनि, यसले केही चुनौतीहरूको पनि सामना गर्छ।
• जटिल प्रक्रिया: प्लाज्मा काट्ने प्रक्रिया जटिल छ र यसलाई सुनिश्चित गर्न उच्च-परिशुद्धता उपकरण र अनुभवी अपरेटरहरू आवश्यक पर्दछकाटनमा शुद्धता र स्थिरता।
• वातावरणीय नियन्त्रण र सुरक्षा: प्लाज्मा बीमको उच्च-तापमान, उच्च-ऊर्जा प्रकृतिको लागि कडा वातावरणीय नियन्त्रण र सुरक्षा उपायहरू आवश्यक पर्दछ, जसले कार्यान्वयनको जटिलता र लागत बढाउँछ।
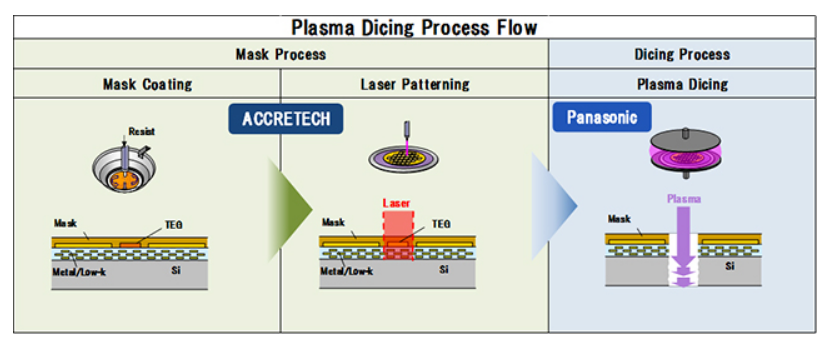
भविष्यको विकास दिशाहरू
प्राविधिक प्रगतिसँगै, प्लाज्मा काट्नेसँग सम्बन्धित चुनौतीहरू बिस्तारै पार हुने अपेक्षा गरिएको छ। स्मार्ट र अधिक स्थिर काट्ने उपकरणहरू विकास गरेर, म्यानुअल सञ्चालनमा निर्भरता कम गर्न सकिन्छ, जसले गर्दा उत्पादन दक्षतामा सुधार हुन्छ। साथै, प्रक्रिया प्यारामिटरहरू र काट्ने वातावरणलाई अनुकूलन गर्नाले सुरक्षा जोखिम र सञ्चालन लागत कम गर्न मद्दत गर्नेछ।
अर्धचालक उद्योगमा, वेफर कटिङ र डाइसिङ प्रविधिमा भएका आविष्कारहरू उद्योगको विकासलाई अगाडि बढाउन महत्त्वपूर्ण छन्। उच्च परिशुद्धता, दक्षता र जटिल वेफर आकारहरू ह्यान्डल गर्ने क्षमताको साथ प्लाज्मा कटिङ प्रविधि यस क्षेत्रमा एक महत्त्वपूर्ण नयाँ खेलाडीको रूपमा देखा परेको छ। यद्यपि केही चुनौतीहरू बाँकी छन्, यी मुद्दाहरूलाई निरन्तर प्राविधिक नवप्रवर्तनका साथ बिस्तारै सम्बोधन गरिनेछ, जसले अर्धचालक निर्माणमा थप सम्भावनाहरू र अवसरहरू ल्याउँछ।
प्लाज्मा काट्ने प्रविधिको प्रयोगको सम्भावना विशाल छ, र यसले भविष्यमा अर्धचालक निर्माणमा अझ महत्त्वपूर्ण भूमिका खेल्ने अपेक्षा गरिएको छ। निरन्तर प्राविधिक नवप्रवर्तन र अनुकूलन मार्फत, प्लाज्मा काट्नेले अवस्थित चुनौतीहरूलाई मात्र सम्बोधन गर्दैन तर अर्धचालक उद्योगको विकासको एक शक्तिशाली चालक पनि बन्नेछ।
२.४ गुणस्तर कटौती र प्रभाव पार्ने कारकहरू
पछिको चिप प्याकेजिङ, परीक्षण, र अन्तिम उत्पादनको समग्र प्रदर्शन र विश्वसनीयताको लागि वेफर काट्ने गुणस्तर महत्त्वपूर्ण छ। काट्ने क्रममा सामना गर्ने सामान्य समस्याहरूमा दरार, चिपिङ, र काट्ने विचलनहरू समावेश छन्। यी समस्याहरू सँगै काम गर्ने धेरै कारकहरूद्वारा प्रभावित हुन्छन्।
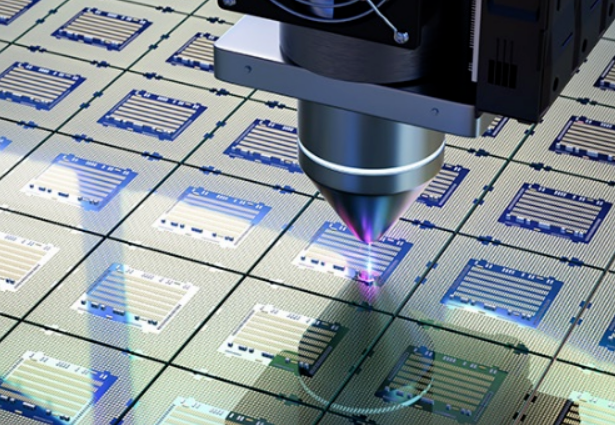
कोटी | सामग्रीहरू | प्रभाव |
प्रक्रिया प्यारामिटरहरू | काट्ने गति, फिड दर, र काट्ने गहिराईले काट्ने प्रक्रियाको स्थिरता र शुद्धतालाई प्रत्यक्ष असर गर्छ। अनुचित सेटिङहरूले तनाव एकाग्रता र अत्यधिक ताप-प्रभावित क्षेत्र निम्त्याउन सक्छ, जसको परिणामस्वरूप दरार र चिपिङ हुन्छ। वेफर सामग्री, मोटाई, र काट्ने आवश्यकताहरूको आधारमा उचित रूपमा प्यारामिटरहरू समायोजन गर्नु इच्छित काट्ने परिणामहरू प्राप्त गर्नको लागि महत्वपूर्ण छ। | सही प्रक्रिया प्यारामिटरहरूले सटीक काट्ने सुनिश्चित गर्दछ र दरार र चिप्स जस्ता दोषहरूको जोखिम कम गर्दछ। |
उपकरण र भौतिक कारकहरू | -ब्लेड गुणस्तर: ब्लेडको सामग्री, कठोरता र पहिरन प्रतिरोधले काट्ने प्रक्रियाको सहजता र काटिएको सतहको समतलतालाई प्रभाव पार्छ। कम गुणस्तरको ब्लेडले घर्षण र थर्मल तनाव बढाउँछ, जसले गर्दा चिरा पर्ने वा चिप्लिने सम्भावना हुन्छ। सही ब्लेड सामग्री छनौट गर्नु महत्त्वपूर्ण छ। -शीतलक प्रदर्शन: कूलेन्टहरूले काट्ने तापक्रम घटाउन, घर्षण कम गर्न र फोहोर हटाउन मद्दत गर्छन्। अप्रभावी कूलेन्टले उच्च तापक्रम र फोहोर जम्मा हुन सक्छ, जसले काट्ने गुणस्तर र दक्षतालाई असर गर्छ। कुशल र वातावरणमैत्री कूलेन्टहरू छनौट गर्नु महत्त्वपूर्ण छ। | ब्लेडको गुणस्तरले काट्ने प्रक्रियाको शुद्धता र सहजतालाई असर गर्छ। अप्रभावी शीतलकले काट्ने गुणस्तर र दक्षतामा कमी ल्याउन सक्छ, जसले गर्दा शीतलकको इष्टतम प्रयोगको आवश्यकतालाई प्रकाश पार्छ। |
प्रक्रिया नियन्त्रण र गुणस्तर निरीक्षण | -प्रक्रिया नियन्त्रण: काट्ने प्रक्रियामा स्थिरता र स्थिरता सुनिश्चित गर्न प्रमुख काट्ने प्यारामिटरहरूको वास्तविक-समय अनुगमन र समायोजन। -गुणस्तर निरीक्षण: काट्ने पछिको उपस्थिति जाँच, आयामी मापन, र विद्युतीय कार्यसम्पादन परीक्षणले गुणस्तर समस्याहरू तुरुन्तै पहिचान गर्न र सम्बोधन गर्न मद्दत गर्दछ, काट्ने शुद्धता र स्थिरतामा सुधार गर्दछ। | उचित प्रक्रिया नियन्त्रण र गुणस्तर निरीक्षणले निरन्तर, उच्च-गुणस्तरको काटन परिणामहरू र सम्भावित समस्याहरूको प्रारम्भिक पहिचान सुनिश्चित गर्न मद्दत गर्दछ। |

काट्ने गुणस्तर सुधार गर्दै
काटन गुणस्तर सुधार गर्न प्रक्रिया प्यारामिटरहरू, उपकरण र सामग्री चयन, प्रक्रिया नियन्त्रण, र निरीक्षणलाई ध्यानमा राखेर व्यापक दृष्टिकोण आवश्यक पर्दछ। काटन प्रविधिहरूलाई निरन्तर परिष्कृत गरेर र प्रक्रिया विधिहरूलाई अनुकूलन गरेर, वेफर काटनको शुद्धता र स्थिरतालाई अझ बढाउन सकिन्छ, जसले अर्धचालक निर्माण उद्योगको लागि थप भरपर्दो प्राविधिक सहयोग प्रदान गर्दछ।
#०३ पोस्ट-कटिङ ह्यान्डलिङ र परीक्षण
३.१ सफाई र सुकाउने
वेफर काट्ने पछि सफा गर्ने र सुकाउने चरणहरू चिपको गुणस्तर र त्यसपछिका प्रक्रियाहरूको सहज प्रगति सुनिश्चित गर्न महत्त्वपूर्ण हुन्छन्। यस चरणमा, काट्ने क्रममा उत्पन्न हुने सिलिकन मलबे, शीतलक अवशेष र अन्य दूषित पदार्थहरूलाई राम्ररी हटाउनु आवश्यक छ। सफाई प्रक्रियाको क्रममा चिप्सलाई क्षति नपुगोस् भन्ने कुरा सुनिश्चित गर्नु पनि उत्तिकै महत्त्वपूर्ण छ, र सुकाएपछि, क्षरण वा इलेक्ट्रोस्टेटिक डिस्चार्ज जस्ता समस्याहरू रोक्न चिपको सतहमा कुनै ओसिलोपन नराख्ने कुरा सुनिश्चित गर्नुहोस्।
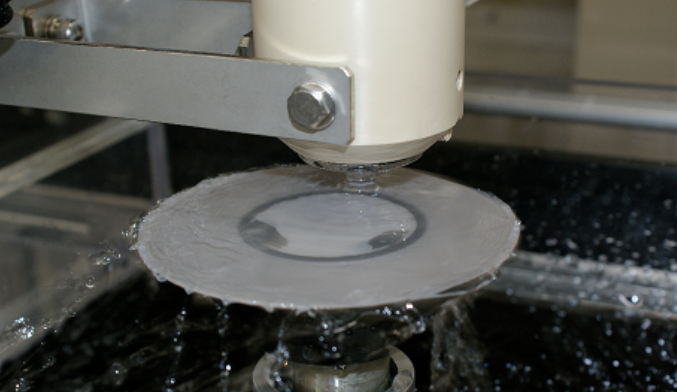
काट्ने पछिको ह्यान्डलिङ: सफाई र सुकाउने प्रक्रिया
प्रक्रिया चरण | सामग्रीहरू | प्रभाव |
सफाई प्रक्रिया | -विधि: सफाईको लागि विशेष सफाई एजेन्टहरू र शुद्ध पानी प्रयोग गर्नुहोस्, अल्ट्रासोनिक वा मेकानिकल ब्रशिङ प्रविधिहरूसँग मिलाउनुहोस्। | दूषित पदार्थहरूलाई पूर्ण रूपमा हटाउने सुनिश्चित गर्दछ र सफाईको क्रममा चिप्समा हुने क्षतिलाई रोक्छ। |
-सफाई एजेन्टको छनोट: चिपलाई नोक्सान नगरी प्रभावकारी सफाई सुनिश्चित गर्न वेफर सामग्री र दूषित पदार्थको प्रकारको आधारमा छनौट गर्नुहोस्। | प्रभावकारी सफाई र चिप सुरक्षाको लागि उचित एजेन्ट चयन महत्वपूर्ण छ। | |
-प्यारामिटर नियन्त्रण: अनुचित सफाईको कारणले हुने गुणस्तर समस्याहरू रोक्न सफाईको तापक्रम, समय र सफाई घोलको सांद्रतालाई कडाइका साथ नियन्त्रण गर्नुहोस्। | नियन्त्रणहरूले वेफरलाई क्षति पुर्याउन वा दूषित पदार्थहरू पछाडि छोड्नबाट जोगिन मद्दत गर्दछ, जसले गर्दा गुणस्तर स्थिर रहन्छ। | |
सुकाउने प्रक्रिया | -परम्परागत विधिहरू: प्राकृतिक हावा सुकाउने र तातो हावा सुकाउने, जसको दक्षता कम हुन्छ र स्थिर बिजुली निर्माण हुन सक्छ। | सुकाउने समय ढिलो हुन सक्छ र सम्भावित स्थिर समस्याहरू हुन सक्छ। |
-आधुनिक प्रविधिहरू: चिप्स छिटो सुक्न र हानिकारक प्रभावहरूबाट बच्न भ्याकुम सुकाउने र इन्फ्रारेड सुकाउने जस्ता उन्नत प्रविधिहरू प्रयोग गर्नुहोस्। | छिटो र अधिक कुशल सुकाउने प्रक्रिया, स्थिर डिस्चार्ज वा आर्द्रता-सम्बन्धित समस्याहरूको जोखिम कम गर्दै। | |
उपकरण चयन र मर्मतसम्भार | -उपकरण चयन: उच्च-कार्यक्षमता सफाई र सुकाउने मेसिनहरूले प्रशोधन दक्षतामा सुधार गर्छन् र ह्यान्डलिङको क्रममा सम्भावित समस्याहरूलाई राम्ररी नियन्त्रण गर्छन्। | उच्च-गुणस्तरका मेसिनहरूले राम्रो प्रशोधन सुनिश्चित गर्छन् र सफाई र सुकाउने क्रममा त्रुटिहरूको सम्भावना कम गर्छन्। |
-उपकरण मर्मतसम्भार: उपकरणको नियमित निरीक्षण र मर्मतसम्भारले यो इष्टतम काम गर्ने अवस्थामा रहन्छ, चिपको गुणस्तर सुनिश्चित गर्दछ। | उचित मर्मतसम्भारले उपकरणको विफलतालाई रोक्छ, भरपर्दो र उच्च-गुणस्तरको प्रशोधन सुनिश्चित गर्दछ। |
काट्ने पछिको सफाई र सुकाउने
वेफर काट्ने पछि सफा गर्ने र सुकाउने चरणहरू जटिल र नाजुक प्रक्रियाहरू हुन् जसलाई अन्तिम प्रशोधन परिणाम सुनिश्चित गर्न धेरै कारकहरूको सावधानीपूर्वक विचार आवश्यक पर्दछ। वैज्ञानिक विधिहरू र कठोर प्रक्रियाहरू प्रयोग गरेर, प्रत्येक चिप इष्टतम अवस्थामा पछिल्ला प्याकेजिङ र परीक्षण चरणहरूमा प्रवेश गर्दछ भनेर सुनिश्चित गर्न सम्भव छ।
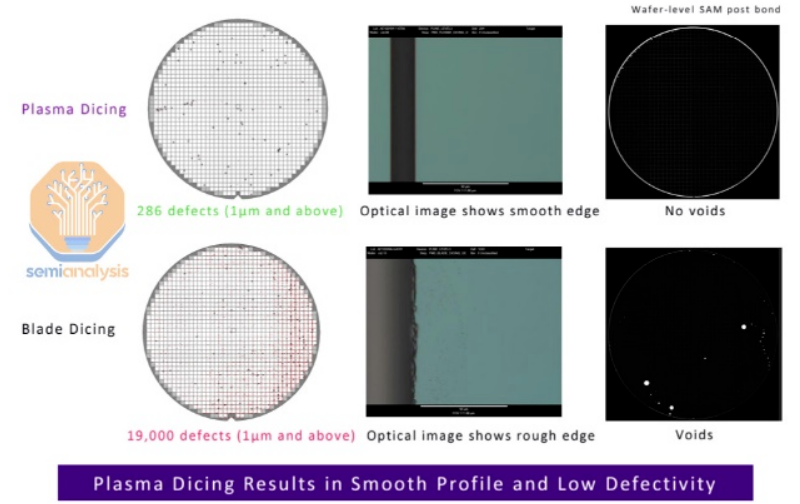
काट्ने पछिको निरीक्षण र परीक्षण
चरण | सामग्रीहरू | प्रभाव |
निरीक्षण चरण | १.दृश्य निरीक्षण: चिपको सतहमा दरार, चिपिङ, वा प्रदूषण जस्ता देखिने दोषहरू जाँच गर्न दृश्यात्मक वा स्वचालित निरीक्षण उपकरण प्रयोग गर्नुहोस्। बर्बादीबाट बच्न भौतिक रूपमा क्षतिग्रस्त चिपहरू द्रुत रूपमा पहिचान गर्नुहोस्। | प्रक्रियाको सुरुवातमा दोषपूर्ण चिप्स पहिचान गर्न र हटाउन मद्दत गर्दछ, जसले गर्दा सामग्रीको क्षति कम हुन्छ। |
२.आकार मापन: चिप आयामहरू सही रूपमा मापन गर्न सटीक मापन उपकरणहरू प्रयोग गर्नुहोस्, कट साइजले डिजाइन विशिष्टताहरू पूरा गर्दछ भनेर सुनिश्चित गर्दै र कार्यसम्पादन समस्याहरू वा प्याकेजिङ कठिनाइहरू रोक्न। | चिप्स आवश्यक आकार सीमा भित्र छन् भनी सुनिश्चित गर्दछ, कार्यसम्पादनमा गिरावट वा एसेम्बली समस्याहरू रोक्न। | |
३.विद्युतीय प्रदर्शन परीक्षण: गैर-अनुपालन चिपहरू पहिचान गर्न र प्रदर्शन-योग्य चिपहरू मात्र अर्को चरणमा जान सुनिश्चित गर्न प्रतिरोध, क्यापेसिटन्स, र इन्डक्टन्स जस्ता प्रमुख विद्युतीय प्यारामिटरहरूको मूल्याङ्कन गर्नुहोस्। | प्रक्रियामा कार्यात्मक र कार्यसम्पादन-परीक्षण गरिएका चिपहरू मात्र अगाडि बढेको सुनिश्चित गर्दछ, जसले गर्दा पछिल्ला चरणहरूमा असफलताको जोखिम कम हुन्छ। | |
परीक्षण चरण | १.कार्यात्मक परीक्षण: चिपको आधारभूत कार्यक्षमताले उद्देश्य अनुसार काम गर्छ कि गर्दैन भनेर प्रमाणित गर्नुहोस्, कार्यात्मक असामान्यताहरू भएका चिपहरू पहिचान गर्ने र हटाउने। | पछिल्ला चरणहरूमा जानु अघि चिप्सले आधारभूत सञ्चालन आवश्यकताहरू पूरा गरेको सुनिश्चित गर्दछ। |
२.विश्वसनीयता परीक्षण: लामो समयसम्म प्रयोग वा कठोर वातावरणमा चिप प्रदर्शन स्थिरताको मूल्याङ्कन गर्नुहोस्, जसमा सामान्यतया उच्च-तापमान बुढ्यौली, कम-तापमान परीक्षण, र आर्द्रता परीक्षण समावेश हुन्छ जसले वास्तविक-विश्व चरम अवस्थाहरूको अनुकरण गर्दछ। | चिप्सले विभिन्न वातावरणीय परिस्थितिहरूमा भरपर्दो रूपमा काम गर्न सक्छ भनी सुनिश्चित गर्दछ, जसले गर्दा उत्पादनको दीर्घायु र स्थिरतामा सुधार हुन्छ। | |
३.अनुकूलता परीक्षण: चिपले अन्य कम्पोनेन्ट वा प्रणालीहरूसँग राम्ररी काम गर्छ कि गर्दैन भनी प्रमाणित गर्नुहोस्, असंगतिको कारणले गर्दा कुनै त्रुटि वा कार्यसम्पादनमा गिरावट आएको छैन भनी सुनिश्चित गर्नुहोस्। | अनुकूलता समस्याहरू रोकेर वास्तविक-विश्व अनुप्रयोगहरूमा सहज सञ्चालन सुनिश्चित गर्दछ। |
३.३ प्याकेजिङ र भण्डारण
वेफर काट्ने पछि, चिप्स अर्धचालक उत्पादन प्रक्रियाको एक महत्वपूर्ण उत्पादन हो, र तिनीहरूको प्याकेजिङ र भण्डारण चरणहरू उत्तिकै महत्त्वपूर्ण छन्। उचित प्याकेजिङ र भण्डारण उपायहरू ढुवानी र भण्डारणको समयमा चिप्सको सुरक्षा र स्थिरता सुनिश्चित गर्न मात्र होइन तर पछिको उत्पादन, परीक्षण र प्याकेजिङ चरणहरूको लागि बलियो समर्थन प्रदान गर्न पनि आवश्यक छ।
निरीक्षण र परीक्षण चरणहरूको सारांश:
वेफर काट्ने पछि चिप्सको निरीक्षण र परीक्षण चरणहरूले दृश्य निरीक्षण, आकार मापन, विद्युतीय प्रदर्शन परीक्षण, कार्यात्मक परीक्षण, विश्वसनीयता परीक्षण, र अनुकूलता परीक्षण सहित विभिन्न पक्षहरूलाई समेट्छ। यी चरणहरू एकअर्कामा जोडिएका र पूरक छन्, जसले उत्पादनको गुणस्तर र विश्वसनीयता सुनिश्चित गर्न ठोस अवरोध बनाउँछ। कडा निरीक्षण र परीक्षण प्रक्रियाहरू मार्फत, सम्भावित समस्याहरू पहिचान गर्न सकिन्छ र तुरुन्तै समाधान गर्न सकिन्छ, अन्तिम उत्पादनले ग्राहकको आवश्यकताहरू र अपेक्षाहरू पूरा गर्दछ भनी सुनिश्चित गर्दै।
पक्ष | सामग्रीहरू |
प्याकेजिङ उपायहरू | १.एन्टी-स्टेटिक: प्याकेजिङ सामग्रीहरूमा उत्कृष्ट एन्टी-स्टेटिक गुणहरू हुनुपर्छ जसले गर्दा स्थिर बिजुलीले उपकरणहरूलाई क्षति पुर्याउन वा तिनीहरूको कार्यसम्पादनलाई असर गर्नबाट जोगाउँछ। |
२.ओसिलोपन प्रतिरोधी: प्याकेजिङ सामग्रीहरूमा आर्द्रताको कारणले हुने क्षरण र विद्युतीय कार्यसम्पादनमा गिरावट रोक्नको लागि राम्रो आर्द्रता प्रतिरोध हुनुपर्छ। | |
३.झट्का प्रतिरोधी: प्याकेजिङ सामग्रीहरूले ढुवानीको समयमा चिप्सलाई कम्पन र प्रभावबाट जोगाउन प्रभावकारी झट्का अवशोषण प्रदान गर्नुपर्छ। | |
भण्डारण वातावरण | १.आर्द्रता नियन्त्रण: अत्यधिक आर्द्रता वा कम आर्द्रताका कारण स्थिर समस्याहरूबाट हुने आर्द्रता अवशोषण र क्षरण रोक्नको लागि उपयुक्त दायरा भित्र आर्द्रतालाई कडाइका साथ नियन्त्रण गर्नुहोस्। |
२.सरसफाइ: धुलो र अशुद्धताबाट चिप्स दूषित हुनबाट जोगाउन सफा भण्डारण वातावरण कायम राख्नुहोस्। | |
३.तापक्रम नियन्त्रण: कम तापक्रमका कारण अत्यधिक गर्मी वा संघनन समस्याका कारण द्रुत बुढ्यौली रोक्न उचित तापक्रम दायरा सेट गर्नुहोस् र तापक्रम स्थिरता कायम राख्नुहोस्। | |
नियमित निरीक्षण | समयमै सम्भावित समस्याहरू पहिचान गर्न र सम्बोधन गर्न दृश्य निरीक्षण, आकार मापन, र विद्युतीय कार्यसम्पादन परीक्षणहरू प्रयोग गरेर भण्डारण गरिएका चिपहरूको नियमित रूपमा निरीक्षण र मूल्याङ्कन गर्नुहोस्। भण्डारण समय र अवस्थाहरूको आधारमा, चिपहरूको प्रयोगको योजना बनाउनुहोस् ताकि तिनीहरू इष्टतम अवस्थामा प्रयोग भएको सुनिश्चित होस्। |
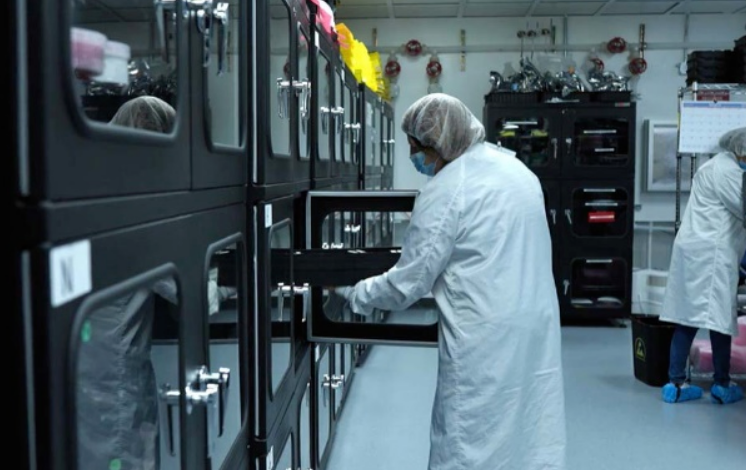
वेफर डाइसिङ प्रक्रियाको क्रममा माइक्रोक्र्याक्स र क्षतिको समस्या अर्धचालक निर्माणमा एक महत्त्वपूर्ण चुनौती हो। काट्ने तनाव यस घटनाको मुख्य कारण हो, किनकि यसले वेफर सतहमा स-साना दरार र क्षति सिर्जना गर्दछ, जसले गर्दा उत्पादन लागत बढ्छ र उत्पादनको गुणस्तरमा कमी आउँछ।
यस चुनौतीलाई सम्बोधन गर्न, काट्ने तनावलाई कम गर्नु र अनुकूलित काट्ने प्रविधि, उपकरणहरू र अवस्थाहरू लागू गर्नु महत्त्वपूर्ण छ। ब्लेड सामग्री, काट्ने गति, दबाब, र शीतलन विधिहरू जस्ता कारकहरूमा सावधानीपूर्वक ध्यान दिनाले माइक्रोक्र्याक्सको गठन कम गर्न र प्रक्रियाको समग्र उपज सुधार गर्न मद्दत गर्न सक्छ। थप रूपमा, लेजर डाइसिङ जस्ता थप उन्नत काट्ने प्रविधिहरूमा जारी अनुसन्धानले यी समस्याहरूलाई अझ कम गर्ने तरिकाहरू खोजिरहेको छ।
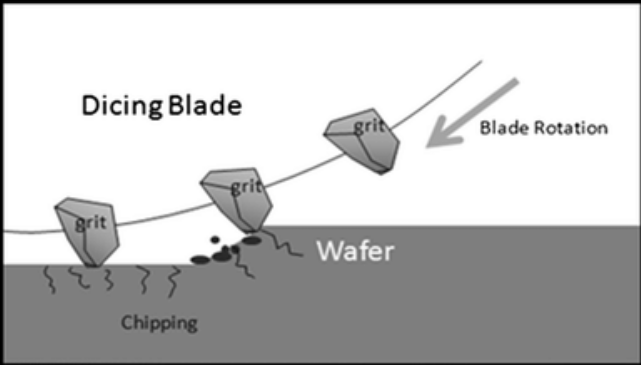
नाजुक सामग्रीको रूपमा, वेफरहरू मेकानिकल, थर्मल वा रासायनिक तनावको अधीनमा हुँदा आन्तरिक संरचनात्मक परिवर्तनहरूको जोखिममा हुन्छन्, जसले गर्दा माइक्रोक्र्याकहरू बन्न सक्छन्। यद्यपि यी दरारहरू तुरुन्तै देखिने नहुन सक्छन्, तिनीहरू विस्तार हुन सक्छन् र उत्पादन प्रक्रिया अगाडि बढ्दै जाँदा थप गम्भीर क्षति पुर्याउन सक्छन्। यो समस्या पछिल्ला प्याकेजिङ र परीक्षण चरणहरूमा विशेष गरी समस्याग्रस्त हुन्छ, जहाँ तापमानमा उतारचढाव र थप मेकानिकल तनावले यी माइक्रोक्र्याकहरू दृश्यात्मक फ्र्याक्चरहरूमा विकसित हुन सक्छन्, सम्भावित रूपमा चिप विफलता निम्त्याउन सक्छ।
यो जोखिम कम गर्न, काट्ने गति, दबाब र तापक्रम जस्ता प्यारामिटरहरूलाई अनुकूलन गरेर काट्ने प्रक्रियालाई सावधानीपूर्वक नियन्त्रण गर्नु आवश्यक छ। लेजर डाइसिङ जस्ता कम आक्रामक काट्ने विधिहरू प्रयोग गर्नाले वेफरमा पर्ने मेकानिकल तनाव कम गर्न सकिन्छ र माइक्रोक्र्याकहरूको गठनलाई कम गर्न सकिन्छ। थप रूपमा, वेफर डाइसिङ प्रक्रियाको क्रममा इन्फ्रारेड स्क्यानिङ वा एक्स-रे इमेजिङ जस्ता उन्नत निरीक्षण विधिहरू लागू गर्नाले यी प्रारम्भिक-चरणका दरारहरूलाई थप क्षति पुर्याउनु अघि पत्ता लगाउन मद्दत गर्न सक्छ।
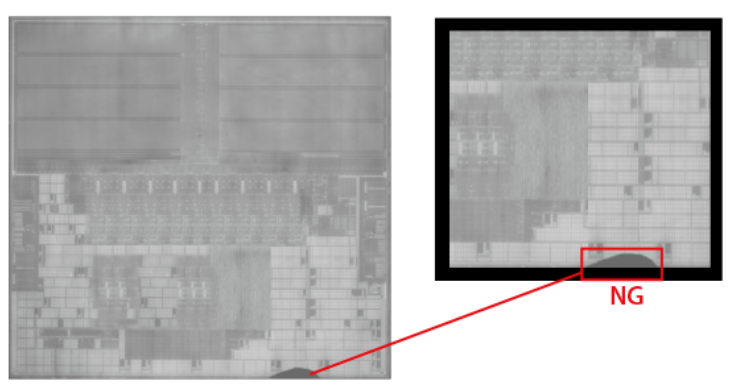
डाइसिङ प्रक्रियामा वेफर सतहमा हुने क्षति एउटा महत्त्वपूर्ण चिन्ताको विषय हो, किनकि यसले चिपको कार्यसम्पादन र विश्वसनीयतामा प्रत्यक्ष प्रभाव पार्न सक्छ। यस्तो क्षति काट्ने उपकरणहरूको अनुचित प्रयोग, गलत काट्ने प्यारामिटरहरू, वा वेफरमा निहित सामग्री दोषहरूको कारणले हुन सक्छ। कारण जेसुकै भए पनि, यी क्षतिहरूले सर्किटको विद्युतीय प्रतिरोध वा क्षमतामा परिवर्तन ल्याउन सक्छ, जसले समग्र कार्यसम्पादनलाई असर गर्छ।
यी समस्याहरूलाई सम्बोधन गर्न, दुई प्रमुख रणनीतिहरूको अन्वेषण भइरहेको छ:
१. काट्ने उपकरण र प्यारामिटरहरू अनुकूलन गर्दै: धारिलो ब्लेडहरू प्रयोग गरेर, काट्ने गति समायोजन गरेर, र काट्ने गहिराइ परिमार्जन गरेर, काट्ने प्रक्रियाको क्रममा तनावको एकाग्रतालाई कम गर्न सकिन्छ, जसले गर्दा क्षतिको सम्भावना कम हुन्छ।
२. नयाँ काट्ने प्रविधिहरूको अन्वेषण: लेजर काट्ने र प्लाज्मा काट्ने जस्ता उन्नत प्रविधिहरूले वेफरमा हुने क्षतिको स्तरलाई सम्भावित रूपमा कम गर्दै सुधारिएको परिशुद्धता प्रदान गर्दछ। वेफरमा थर्मल र मेकानिकल तनाव कम गर्दै उच्च काट्ने शुद्धता प्राप्त गर्ने तरिकाहरू खोज्न यी प्रविधिहरूको अध्ययन भइरहेको छ।
थर्मल प्रभाव क्षेत्र र कार्यसम्पादनमा यसको प्रभाव
लेजर र प्लाज्मा काट्ने जस्ता थर्मल काट्ने प्रक्रियाहरूमा, उच्च तापक्रमले अनिवार्य रूपमा वेफरको सतहमा थर्मल प्रभाव क्षेत्र सिर्जना गर्दछ। यो क्षेत्र, जहाँ तापक्रम ढाँचा महत्त्वपूर्ण छ, सामग्रीको गुणहरू परिवर्तन गर्न सक्छ, चिपको अन्तिम कार्यसम्पादनलाई असर गर्छ।
तापीय प्रभावित क्षेत्र (TAZ) को प्रभाव:
क्रिस्टल संरचना परिवर्तनहरू: उच्च तापक्रममा, वेफर सामग्री भित्रका परमाणुहरू पुन: व्यवस्थित हुन सक्छन्, जसले गर्दा क्रिस्टल संरचनामा विकृतिहरू उत्पन्न हुन्छन्। यो विकृतिले सामग्रीलाई कमजोर बनाउँछ, यसको यान्त्रिक शक्ति र स्थिरता घटाउँछ, जसले प्रयोगको क्रममा चिप विफलताको जोखिम बढाउँछ।
विद्युतीय गुणहरूमा परिवर्तनहरू: उच्च तापक्रमले अर्धचालक सामग्रीहरूमा वाहक सांद्रता र गतिशीलतालाई परिवर्तन गर्न सक्छ, जसले चिपको विद्युतीय चालकता र वर्तमान प्रसारण दक्षतालाई असर गर्छ। यी परिवर्तनहरूले चिपको कार्यसम्पादनमा गिरावट ल्याउन सक्छ, सम्भावित रूपमा यसलाई यसको अभिप्रेत उद्देश्यको लागि अनुपयुक्त बनाउन सक्छ।
यी प्रभावहरूलाई कम गर्न, काट्ने क्रममा तापक्रम नियन्त्रण गर्ने, काट्ने प्यारामिटरहरूलाई अनुकूलन गर्ने, र कूलिंग जेटहरू वा पोस्ट-प्रोसेसिङ उपचार जस्ता विधिहरूको अन्वेषण गर्ने थर्मल प्रभावको हद कम गर्न र सामग्रीको अखण्डता कायम राख्न आवश्यक रणनीतिहरू हुन्।
समग्रमा, वेफर डाइसिङ प्रविधिमा माइक्रोक्र्याक र थर्मल इम्प्याक्ट जोन दुवै महत्वपूर्ण चुनौती हुन्। अर्धचालक उत्पादनहरूको गुणस्तर सुधार गर्न र तिनीहरूको बजार प्रतिस्पर्धात्मकता बढाउन प्राविधिक प्रगति र गुणस्तर नियन्त्रण उपायहरूसँगै निरन्तर अनुसन्धान आवश्यक हुनेछ।
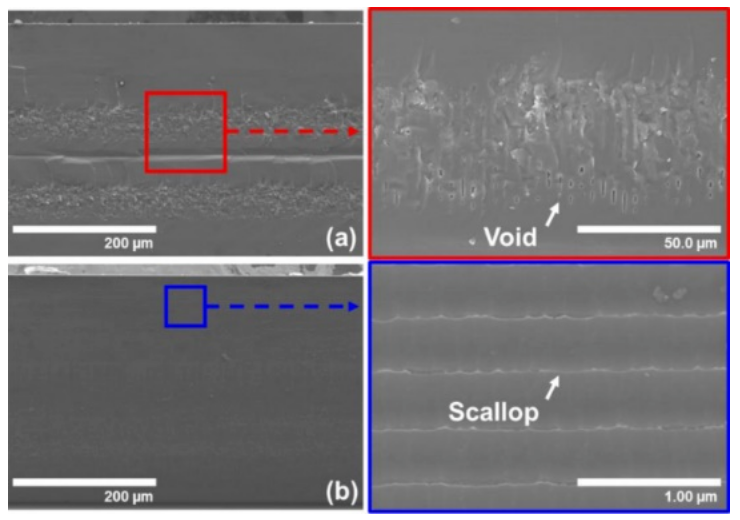
थर्मल इम्प्याक्ट जोन नियन्त्रण गर्ने उपायहरू:
काट्ने प्रक्रिया प्यारामिटरहरू अनुकूलन गर्दै: काट्ने गति र शक्ति घटाउनाले थर्मल इम्प्याक्ट जोन (TAZ) को आकारलाई प्रभावकारी रूपमा कम गर्न सकिन्छ। यसले काट्ने प्रक्रियाको क्रममा उत्पन्न हुने तापको मात्रा नियन्त्रण गर्न मद्दत गर्दछ, जसले वेफरको भौतिक गुणहरूलाई प्रत्यक्ष असर गर्छ।
उन्नत शीतलन प्रविधिहरू: तरल नाइट्रोजन शीतलन र माइक्रोफ्लुइडिक शीतलन जस्ता प्रविधिहरूको प्रयोगले थर्मल प्रभाव क्षेत्रको दायरालाई उल्लेखनीय रूपमा सीमित गर्न सक्छ। यी शीतलन विधिहरूले तापलाई अझ कुशलतापूर्वक नष्ट गर्न मद्दत गर्दछ, यसरी वेफरको भौतिक गुणहरू सुरक्षित राख्छ र थर्मल क्षतिलाई कम गर्छ।
सामग्री चयन: अनुसन्धानकर्ताहरूले कार्बन नानोट्यूब र ग्राफिन जस्ता नयाँ सामग्रीहरूको अन्वेषण गरिरहेका छन्, जसमा उत्कृष्ट थर्मल चालकता र मेकानिकल शक्ति छ। यी सामग्रीहरूले चिप्सको समग्र कार्यसम्पादनमा सुधार गर्दै थर्मल प्रभाव क्षेत्रलाई कम गर्न सक्छन्।
संक्षेपमा, तापीय प्रभाव क्षेत्र तापीय काट्ने प्रविधिहरूको अपरिहार्य परिणाम भएतापनि, यसलाई अनुकूलित प्रशोधन प्रविधिहरू र सामग्री चयन मार्फत प्रभावकारी रूपमा नियन्त्रण गर्न सकिन्छ। भविष्यको अनुसन्धानले अझ कुशल र सटीक वेफर डाइसिङ प्राप्त गर्न थर्मल काट्ने प्रक्रियाहरूलाई फाइन-ट्युनिङ र स्वचालित गर्ने कुरामा ध्यान केन्द्रित गर्नेछ।

सन्तुलन रणनीति:
वेफर डाइसिङ प्रविधिमा वेफरको उपज र उत्पादन दक्षता बीचको इष्टतम सन्तुलन प्राप्त गर्नु निरन्तर चुनौती हो। उत्पादकहरूले तर्कसंगत उत्पादन रणनीति र प्रक्रिया प्यारामिटरहरू विकास गर्न बजारको माग, उत्पादन लागत र उत्पादनको गुणस्तर जस्ता धेरै कारकहरूलाई विचार गर्न आवश्यक छ। साथै, उन्नत काट्ने उपकरणहरूको परिचय, अपरेटर सीप सुधार, र कच्चा मालको गुणस्तर नियन्त्रण बढाउनु उत्पादन दक्षता बढाउँदै उत्पादन कायम राख्न वा सुधार गर्न आवश्यक छ।
भविष्यका चुनौती र अवसरहरू:
अर्धचालक प्रविधिको विकाससँगै, वेफर काट्ने कामले नयाँ चुनौती र अवसरहरूको सामना गर्नुपरेको छ। चिपको आकार घट्दै जाँदा र एकीकरण बढ्दै जाँदा, काट्ने परिशुद्धता र गुणस्तरको मागहरू उल्लेखनीय रूपमा बढ्दै जान्छन्। साथै, उदीयमान प्रविधिहरूले वेफर काट्ने प्रविधिहरूको विकासको लागि नयाँ विचारहरू प्रदान गर्दछन्। उत्पादकहरूले बजारको गतिशीलता र प्राविधिक प्रवृत्तिहरूसँग अभ्यस्त रहनुपर्छ, बजार परिवर्तनहरू र प्राविधिक मागहरू पूरा गर्न उत्पादन रणनीतिहरू र प्रक्रिया प्यारामिटरहरूलाई निरन्तर समायोजन र अनुकूलन गर्दै।
निष्कर्षमा, बजारको माग, उत्पादन लागत, र उत्पादनको गुणस्तरलाई एकीकृत गरेर, र उन्नत उपकरण र प्रविधिको परिचय दिएर, अपरेटर सीपहरू बढाएर, र कच्चा पदार्थ नियन्त्रणलाई सुदृढ पारेर, उत्पादकहरूले वेफर डाइसिङको समयमा वेफर उपज र उत्पादन दक्षता बीचको उत्तम सन्तुलन प्राप्त गर्न सक्छन्, जसले गर्दा कुशल र उच्च-गुणस्तरको अर्धचालक उत्पादन उत्पादन हुन्छ।
भविष्यको दृष्टिकोण:
द्रुत प्राविधिक प्रगतिसँगै, अर्धचालक प्रविधि अभूतपूर्व गतिमा अगाडि बढिरहेको छ। अर्धचालक निर्माणमा एक महत्वपूर्ण चरणको रूपमा, वेफर काट्ने प्रविधि रोमाञ्चक नयाँ विकासहरूको लागि तयार छ। अगाडि हेर्दा, वेफर काट्ने प्रविधिले परिशुद्धता, दक्षता र लागतमा उल्लेखनीय सुधार हासिल गर्ने अपेक्षा गरिएको छ, जसले अर्धचालक उद्योगको निरन्तर वृद्धिमा नयाँ जीवनशक्ति प्रदान गर्दछ।
बढ्दो परिशुद्धता:
उच्च परिशुद्धताको खोजीमा, वेफर काट्ने प्रविधिले निरन्तर अवस्थित प्रक्रियाहरूको सीमालाई धकेल्नेछ। काट्ने प्रक्रियाको भौतिक र रासायनिक संयन्त्रहरूको गहिरो अध्ययन गरेर र काट्ने प्यारामिटरहरूलाई सटीक रूपमा नियन्त्रण गरेर, बढ्दो जटिल सर्किट डिजाइन आवश्यकताहरू पूरा गर्न राम्रो काट्ने परिणामहरू प्राप्त गरिनेछ। थप रूपमा, नयाँ सामग्री र काट्ने विधिहरूको अन्वेषणले उपज र गुणस्तरमा उल्लेखनीय सुधार गर्नेछ।
दक्षता वृद्धि:
नयाँ वेफर काट्ने उपकरणहरू स्मार्ट र स्वचालित डिजाइनमा केन्द्रित हुनेछन्। उन्नत नियन्त्रण प्रणाली र एल्गोरिदमहरूको परिचयले उपकरणहरूलाई विभिन्न सामग्री र डिजाइन आवश्यकताहरू समायोजन गर्न स्वचालित रूपमा काट्ने प्यारामिटरहरू समायोजन गर्न सक्षम बनाउनेछ, जसले गर्दा उत्पादन दक्षतामा उल्लेखनीय सुधार हुनेछ। बहु-वेफर काट्ने प्रविधि र द्रुत ब्लेड प्रतिस्थापन प्रणाली जस्ता नवीनताहरूले दक्षता बढाउन महत्त्वपूर्ण भूमिका खेल्नेछन्।
लागत घटाउने:
वेफर काट्ने प्रविधिको विकासको लागि लागत घटाउनु एक प्रमुख दिशा हो। नयाँ सामग्री र काट्ने विधिहरू विकास हुँदै जाँदा, उपकरण लागत र मर्मत खर्च प्रभावकारी रूपमा नियन्त्रण हुने अपेक्षा गरिएको छ। थप रूपमा, उत्पादन प्रक्रियाहरूलाई अनुकूलन गर्ने र स्क्र्याप दरहरू घटाउनाले उत्पादनको क्रममा फोहोरलाई अझ कम गर्नेछ, जसले गर्दा समग्र उत्पादन लागतमा कमी आउनेछ।
स्मार्ट उत्पादन र IoT:
स्मार्ट उत्पादन र इन्टरनेट अफ थिंग्स (IoT) प्रविधिहरूको एकीकरणले वेफर कटिङ प्रविधिमा परिवर्तनकारी परिवर्तन ल्याउनेछ। उपकरणहरू बीचको अन्तरसम्बन्ध र डेटा साझेदारी मार्फत, उत्पादन प्रक्रियाको प्रत्येक चरणलाई वास्तविक समयमा अनुगमन र अनुकूलित गर्न सकिन्छ। यसले उत्पादन दक्षता र उत्पादन गुणस्तरमा मात्र सुधार गर्दैन तर कम्पनीहरूलाई अझ सटीक बजार पूर्वानुमान र निर्णय लिने समर्थन पनि प्रदान गर्दछ।
भविष्यमा, वेफर काट्ने प्रविधिले परिशुद्धता, दक्षता र लागतमा उल्लेखनीय प्रगति गर्नेछ। यी प्रगतिहरूले अर्धचालक उद्योगको निरन्तर विकासलाई अगाडि बढाउनेछन् र मानव समाजमा थप प्राविधिक आविष्कार र सुविधा ल्याउनेछन्।
पोस्ट समय: नोभेम्बर-१९-२०२४